Thingiverse is a vast online collection of free 3D printable models ready to download and print. It has figurines, planters, and spare parts for home appliances, and the best part is that you don’t need a 3D printer to get these parts. Just upload them to a 3D printing service, and in just a few steps, the part will be at your doorstep.
You will need to locate one because Thingiverse is not a 3D printing service and no longer provides a direct link to 3D printing services. We’ve done the work for you, putting the top services to the test on two Thingiverse models.
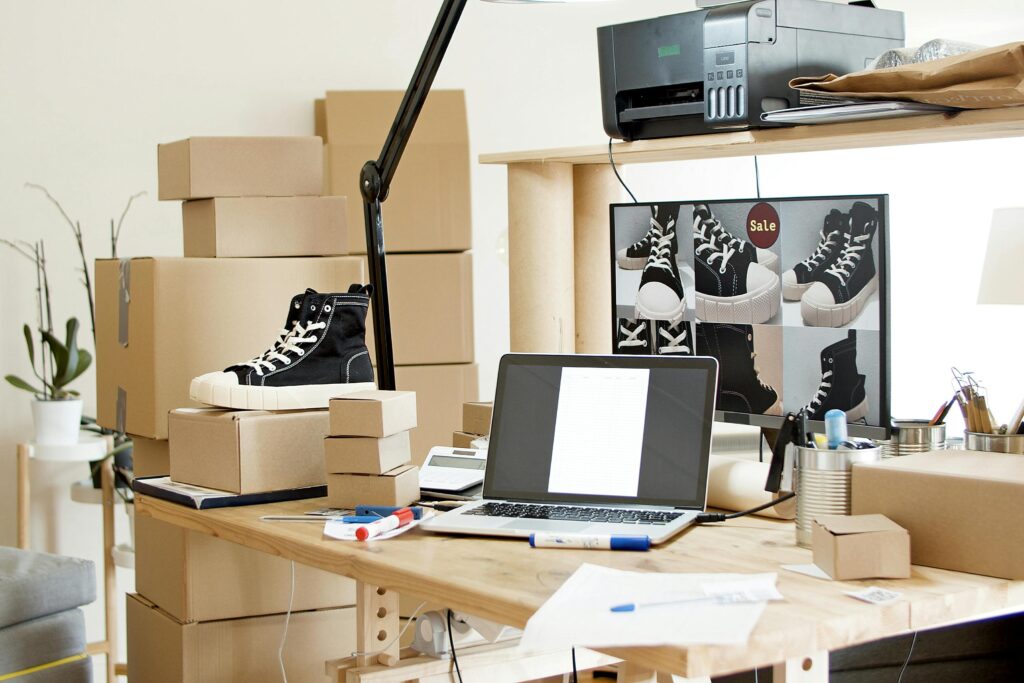
Signing up for a Thingiverse account is all you need to get started with 3D printing from Thingiverse. After that, you can look through collections of 3D-printed models or search for a particular part you need. Maybe you’re a teacher looking for a model dinosaur, a parent who wants to gift their child a 3D-printed Millennium Falcon, or you’re just looking for the right gadget to fit your home at a reasonable price.
We put two of these Thingiverse designs to the test to demonstrate the possibilities because figurines and useful household items are the most frequently printed items on the platform. BEST 3D PRINTING SERVICES FOR THINGIVERSE THINGS
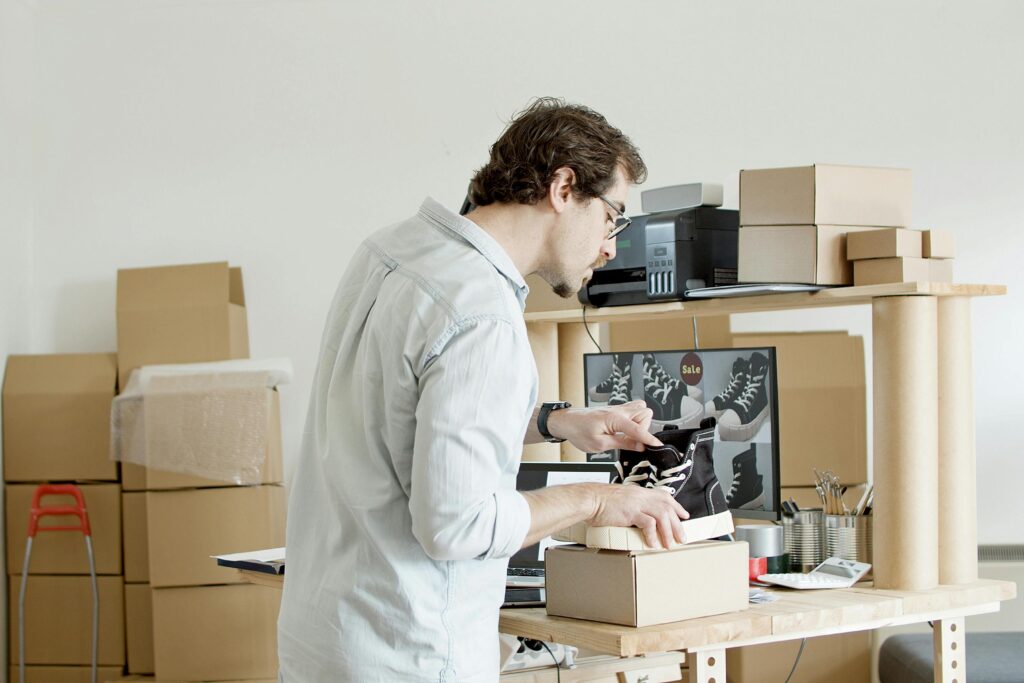
Preparing the Thing
First things first, you’ll need to download the files for your chosen model. On Thingiverse, you have the option of creating an account to save the models you like and the ability to save your Things in organized folders. If you want to print multiple models without having to open a tab for each one, this will come in handy. You can save the models and return later to download them and print them if you have an account. Download the necessary files from the “Thing Files” tab when you are prepared. They usually come in a zipped folder, which you’ll need to unzip into a different folder.
Complex objects frequently consist of multiple printed parts that are assembled after printing. Keep this in mind, as each individual piece will be treated as a separate print. To start, you may want to keep it simple with a model that has just one piece. This was the case for our test files—all we had to do was download one STL file for each model.
If your model has multiple files attached to it, search for the STL files once they’re downloaded. Each item that needs to be printed will have one. There will also be a JPG picture of each object, a readme file, and a license file. You can ignore everything that isn’t an STL.
Some files on Thingiverse may also come in 3MF format. Some 3D printing services don’t support the 3MF file format, but all of them will support an STL file.
The selection of a technology proper for our project is sometimes one of the most difficult decisions we make. A wide scope of completely different 3D printing methods forces a question: what are the greatest differences between the specific 3D printers, and which specialty materials available on the market will be the best? The last but not least question is obviously the one about the price of 3D printing in the technology we have selected.
The most frequently chosen technologies are Fused Deposition Modeling (FDM), Stereolithography (SLA), Selective Laser Sintering (SLS), PolyJet, and Direct Metal Laser Sintering (DMLS). The proper application of those five 3D printing solutions guarantees the achievement of the most important advantages related to such printing.
Five 3D printing technologies
1. Fused Deposition Modeling (FDM) and Fused Filament Fabrication (FFF): 3D printing in FDM/FFF technology is one of the oldest and most widespread additive methods in the world. It consists of depositing the subsequent layers of fused material and letting the adjacent layers cool and merge with each other before another layer is deposited.
The FDM technology may be described as a process reverse to CNC numerical cutting. 3D models are transformed into G-codes being sets of instructions. They serve the positioning of drivers, thus making precise extrusions for the purpose of creating another layer. The technology mostly uses an exact quantity of material required for the specific part, unlike CNC methods, which generate high losses of the material we use.
FFF or FDM technology resolution
The resolution of high prototyping is affected by many factors, such as accuracy of drivers positioning, calibration by the user, or quality of material applied in FDM 3D printing. The tolerance for FDM printing typically ranges from 0.15 mm to 0.25 mm. Where is FFF or FDM technology applied?
The greatest FDM advantages include fast adjustment of the filling of the printed 3D models. This means that it is very easy to print a prototype only for checking the adjustment and finishing. With low internal filling, or even a hollow core, we save on the cost of material. With the design phase finished, we may carry out final control or launch small or medium-sized production series with the final filling of the respective 3D print.
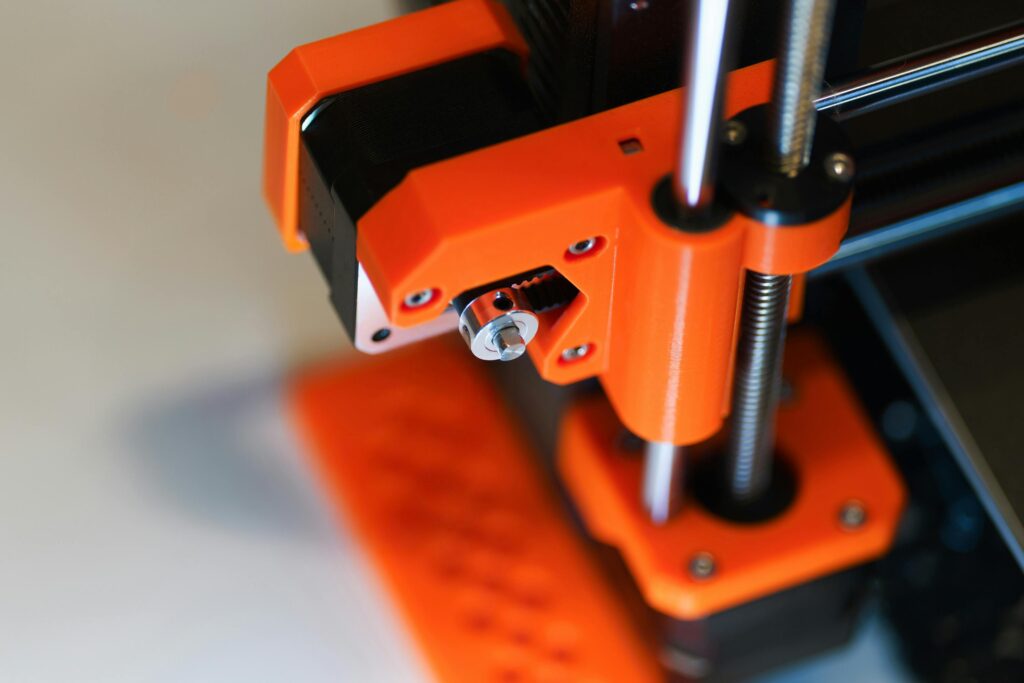
FFF is the most optimal method of fast prototyping of parts that must keep the standard tolerance. The method has been widely used in creating architectural or model mock-ups. The technology guarantees affordable prices and short lead times.
Part 3D printed with the use of FDM technology
2. Selective Laser Sintering (SLS):
SLS consists of merging polyamide particles with the use of a high-energy laser beam. The process starts with the chamber filling with powdered material. Along with the progress of printing, the working surface lowers, and another layer of powder is added. Sintering of the polyamide powder takes place carefully, layer by layer. The 3D SLS technology does not require any supports to be applied because models are naturally supported by the excess of powdered material that closely surrounds the printout. The solution enables the manufacturing of geometrically complex elements with high dimensional accuracy, compared to other 3D printing methods.
Wide range of SLS materials
SLS is particularly interesting with regard to the use of materials that are broadly applied in the plastics industry, including polyamides. In that technology, we may print, for example, from a flame-resistant PA 2241 FR material assigned the German certificate of CS 25/JAR 25/FAR 25 § 25-853 (a) App. Part I of F, ABD 0031. Powdered glass is added to the PA 3200 GF (glass fiber) for elements that require more rigidity. The materials most frequently used in industry also include PA 12 (PA 2200).
3D printing of large models
SLS devices mostly used in those 3D printing methods have working chambers of the size 340 x 240 x 600 mm, which enables printing quite large elements or hundreds of smaller pieces in a series, ensuring a high level of repeatability offered by Selective Laser Sintering. The SLS technology guarantees 0.15 mm tolerance.
Consult your project with 3D printing experts.
30 years of nickel and chromium).