A new UK-based collaboration uses 3D printing to change how bioreactors are made and used, focusing on reducing waste and making the biopharma industry greener.
Launched with £1.9 million ($2.5 million) in funding from the UK government’s agency supporting new technologies, Innovate UK, Project Nexus brings together a team of researchers and companies to create greener, reusable versions of single-use bioprocessing equipment, such as bioreactors.
While traditional bioreactors can be large, permanent stainless-steel systems used in full-scale drug manufacturing, smaller single-use bioreactors are often made of plastic and commonly used in research labs and early-stage production. These disposable units range from just a few liters to a couple hundred liters. They’re faster to set up, eliminate the need for complex sterilization routines, and make it easy to test different drug formulas without cross-contamination. But once used, they’re usually thrown away. Even though they make up only a small portion of global plastic waste, their increasing use has raised concerns about long-term sustainability.
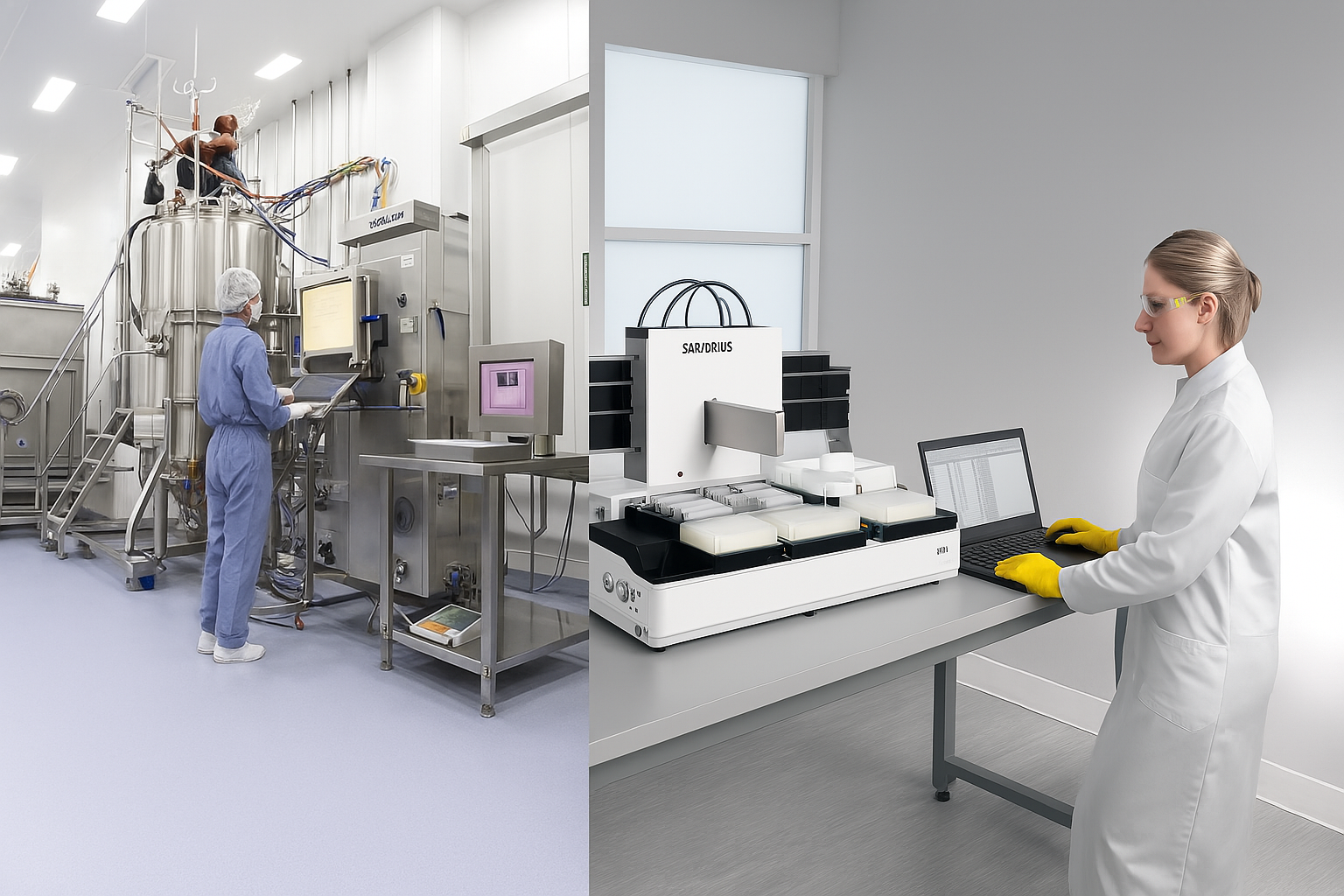
Left: large-scale bioreactor. Right: single-use bioreactor. Images courtesy of WuXi Biologics/Sartorius.
Project Nexus wants to tackle this issue by rethinking how these tools are made and what they’re made from. The group includes 3D printing specialists Photocentric, known for its resin-based printers, and Sartorius, a major supplier of lab and bioprocessing tools. Metamorphic brings expertise in advanced digital design for manufacturing, while the Centre for Process Innovation (CPI) focuses on developing sustainable materials. Academic research support comes from Imperial College London and the University of Sheffield‘s Advanced Manufacturing Research Centre (AMRC).
Why 3D Printing?
3D printing offers major advantages in this space. It allows highly customized parts to be made without traditional molds or tooling, like the media contact devices that sit inside bioreactors and monitor the cell cultures using spectroscopy. These parts must be chemically stable, resistant to high temperatures, and compatible with living cells. 3D printing lets designers customize these shapes while reducing the need for large molds or assembly lines. It also opens the door to creating only what’s needed, cutting down on waste.
A key part of Project Nexus is combining 3D printing with newly developed bio-based materials, making some parts reusable. The project aims to make parts that can be cleaned and reused using high-heat sterilization so they still offer the convenience of single-use systems but with less waste.

CAD rendering of a 3D printed media contact device used to continuously monitor media within a bioreactor via spectroscopy. Image courtesy of Photocentric.
New Resins, New Possibilities
Photocentric, known for its resin-based 3D printers, is supplying its newest system, called JENI, to help create these next-generation tools. JENI is a large, industrial-scale, modular 3D printer for high-speed, high-volume production.
Also, the researchers are working on new sustainable, bio-based thermoset resins that can be printed into shape and then hardened to become strong, stable, and reusable. Thermosets are often difficult to recycle, but the goal is to make them tough enough to go through an autoclave, which uses high heat and pressure to sterilize equipment.
“Our focus on circularity and end-of-life solutions ensures that this project not only advances technological capabilities but also drives meaningful progress towards net zero goals. We look forward to collaborating with our partners to redefine the role of additive manufacturing in the sector,” stated Tony Jackson, director of formulation at CPI.
Big Impacts, Small Waste
Single-use technologies (SUTs) like disposable bioreactors are widely used in biopharma because they’re quick to set up, flexible, and eliminate the need for deep cleaning. They also help save water, energy, and harsh chemicals. But their growing use adds to plastic waste.
Bioreactors like these played a key role in producing Covid-19 vaccines. For example, Pfizer-BioNTech and Moderna used bioreactors to help make the lipid nanoparticles that carry mRNA into the body. Johnson & Johnson used them to grow the cells needed to produce the viral material for its vaccine. In both cases, single-use bioreactors allowed companies to scale production quickly while keeping everything clean and safe.
Project Nexus wants to keep all those benefits while improving sustainability with better materials and reusable parts. While waste from SUTs currently makes up only about 0.002% of global plastic waste, the team sees room for improvement.
What sets this research apart is its full-system approach. Instead of focusing on a single component, the project looks at everything—from materials and manufacturing to reuse and end-of-life plans.
Sartorius brings expertise in equipment manufacturing to biopharma. CPI and Imperial College add strength in materials and process innovation. The AMRC at the University of Sheffield contributes design-for-sustainability know-how. And Photocentric, as always, brings 3D printing firepower.
“The goals at the heart of the Nexus project go beyond simply enabling us to unlock the applications of today,” said Sartorius’s Jeremy Pullin. “They also allow us to realize the future obligations of us all, through the development of sustainable material formulations.”
Tested for the Real World
The components developed through Project Nexus will go through real-world testing. First, they’ll be tested in pharmaceutical research labs and small-scale manufacturing setups, like point-of-care facilities where medicines are made on-site. Later, the team hopes these technologies will move into industrial biotechnology, including green chemical production.
Project Nexus has officially launched and is expected to make progress over the next two years. As the work progresses, researchers will also assess how well the 3D printed parts perform—not just in the lab but economically and environmentally. That includes checking how often a part can be sterilized and reused, whether it lowers costs, and what happens when it reaches the end of its life. The goal is to make sure the new tools aren’t just greener in theory but truly sustainable in practice.
Subscribe to Our Email Newsletter
Stay up-to-date on all the latest news from the 3D printing industry and receive information and offers from third party vendors.