Understanding the Function of 3D Printing in the Fashion, Jewelry, Accessories, and Footwear Industries What if the future of fashion and jewelry wasn’t just sewn, cast, or molded—but printed? Advancements in fabrication have always shaped fashion, jewelry, and accessories, expanding what’s possible in both form and function. 3D printing is now at the center of this evolution, offering designers a precise, flexible, and highly efficient approach to prototyping and production. Originally developed for industrial applications, the technology is now widely used in fashion houses, jewelry ateliers, and independent design studios to create detailed, customizable, and technically sophisticated pieces.
Unlike traditional manufacturing, which often relies on molds, casting, or manual assembly, 3D printing builds layer by layer, allowing for finer details, structural complexity, and design flexibility that would otherwise be difficult or impractical to achieve. The result? More room to experiment, perfect, and expand without sacrificing craftsmanship. This article breaks down how 3D printing is changing fashion, jewelry, and accessories design, from rapid prototyping to finished products. We will explore practical examples, material and technology recommendations, and how designers can leverage these tools to improve their workflow. Additionally, we’ll highlight the key advantages of 3D printing in design iteration, production efficiency, and creative possibilities, along with insights into what this means for the future of the industry.
How is 3D Printing Used in Fashion?
3D printing is becoming a key tool in fashion, primarily for prototyping but also for final garment and accessory production. Designers use it to test concepts, refine details, and push the boundaries of structure and materiality before committing to traditional manufacturing methods.While high-fashion brands integrate 3D-printed elements into couture pieces, the technology is more commonly used in the early stages of design for:

• Before cutting or sewing fabrics, creating prototypes of new shapes and structures. • Testing textures and materials to evaluate how a piece will look and feel before full-scale production.
• Creating detailed embellishments or components that can later be cast or reproduced using traditional techniques.
• Building skeletal structures that fabric is draped over, creating a rigid base for textiles while maintaining flexibility in design.
Iris van Herpen and other high-end fashion designers have pioneered the use of 3D-printed couture, creating garments that are highly architectural and fluid, redefining materiality in fashion. Now for select projects, 3D printing is also used in the final product, particularly for rigid structures, sculptural details, and wearable tech integrations, as seen in high-profile performances and runway shows—Katy Perry’s stage outfits and Victoria’s Secret’s 3D-printed wings are standout examples.
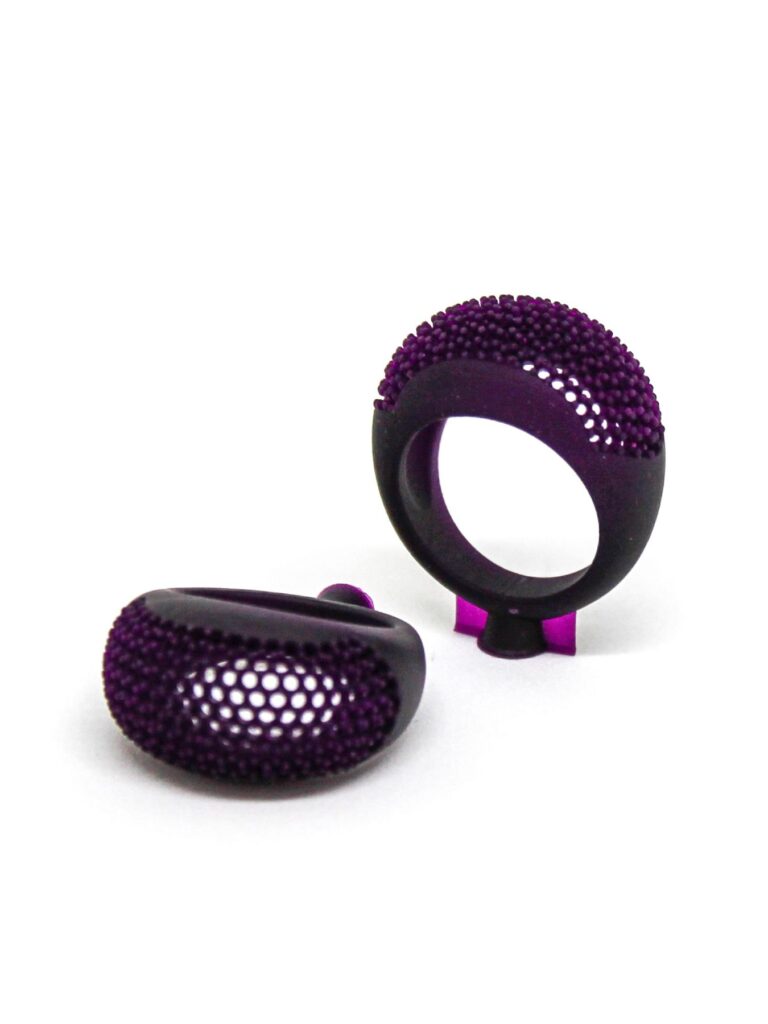
How does jewelry make use of 3D printing? Jewelry designers are increasingly turning to 3D printing as a key tool in both prototyping and production, improving workflows and enabling detailing that would be impractical or time-consuming using traditional methods. Whether for testing a design, refining details, or creating cast-ready models, 3D printing improves precision, reduces lead times, and provides greater flexibility in the creative process.
Jewelry designers employ various 3D printing techniques to enhance their workflows, including:
- Prototyping & Design Validation
Before committing to expensive materials and casting, jewelers use 3D printing to test proportions, fit, and aesthetic details. This allows for quick iterations and client approvals, reducing back-and-forth communication and avoiding costly design errors.
According to Christina Perla, CEO of Makelab, jewelry designers using 3D printing can iterate designs in hours instead of weeks, dramatically improving workflow.
“The ability to refine a design same-day and go straight into production is a pathbreaker for designers looking to innovate quickly.”
- Christina Perla, Co-Founder & CEO at Makelab
Common Materials for Prototyping: • Standard Resin (SLA Technology) – Provides smooth surfaces and fine details, ideal for initial concept models.
• Grey Pro Resin (SLA Technology) – A durable material used for functional testing, ensuring a design holds up underwear.